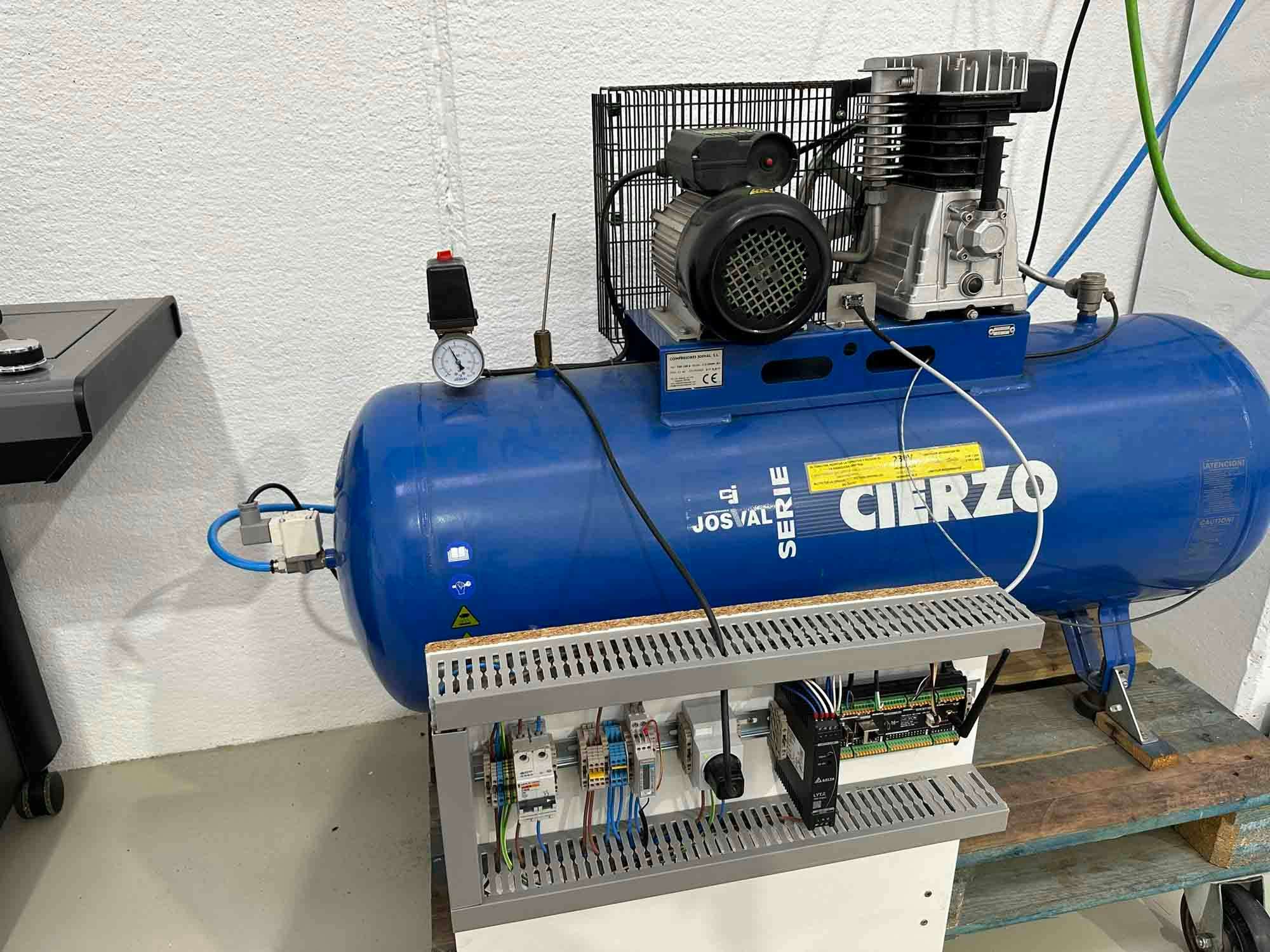
Automotive manufacturers are on the forefront of the Industry 4.0 revolution – and with good reason: their high-standard field is currently facing huge challenges to optimize every single process while maintaining top-quality products. Luckily, at their side they have innovative engineering companies like Engapplic, based in Spain: they are experts at predictive maintenance, process optimization of industrial automation plants and automatic quality inspections – and have chosen Arduino as their technological and strategic partner for a wide range of applications already.
So, when a tier-1 automotive client of theirs asked for a proof of concept to start digitizing their warehouse and workshop, Engapplic came up with a project to monitor air compressors collecting a variety of data and leveraging machine learning to efficiently keep equipment in check 24/7 and in real time, so it can run more efficiently and with less downtime overall.
In this case, Arduino Pro’s Portenta Machine Control was the ideal choice to create a smart solution that is cost-effective and convenient today, and ready for the future of the automotive industry tomorrow.
“Compared to traditional PLCs on the market, Portenta Machine Control allowed us to minimize the footprint in a really cost-effective way. It gave us all the connectivity we needed. And it’s future-proof”
Rubén Moreno, co-founder and project manager at Engapplic
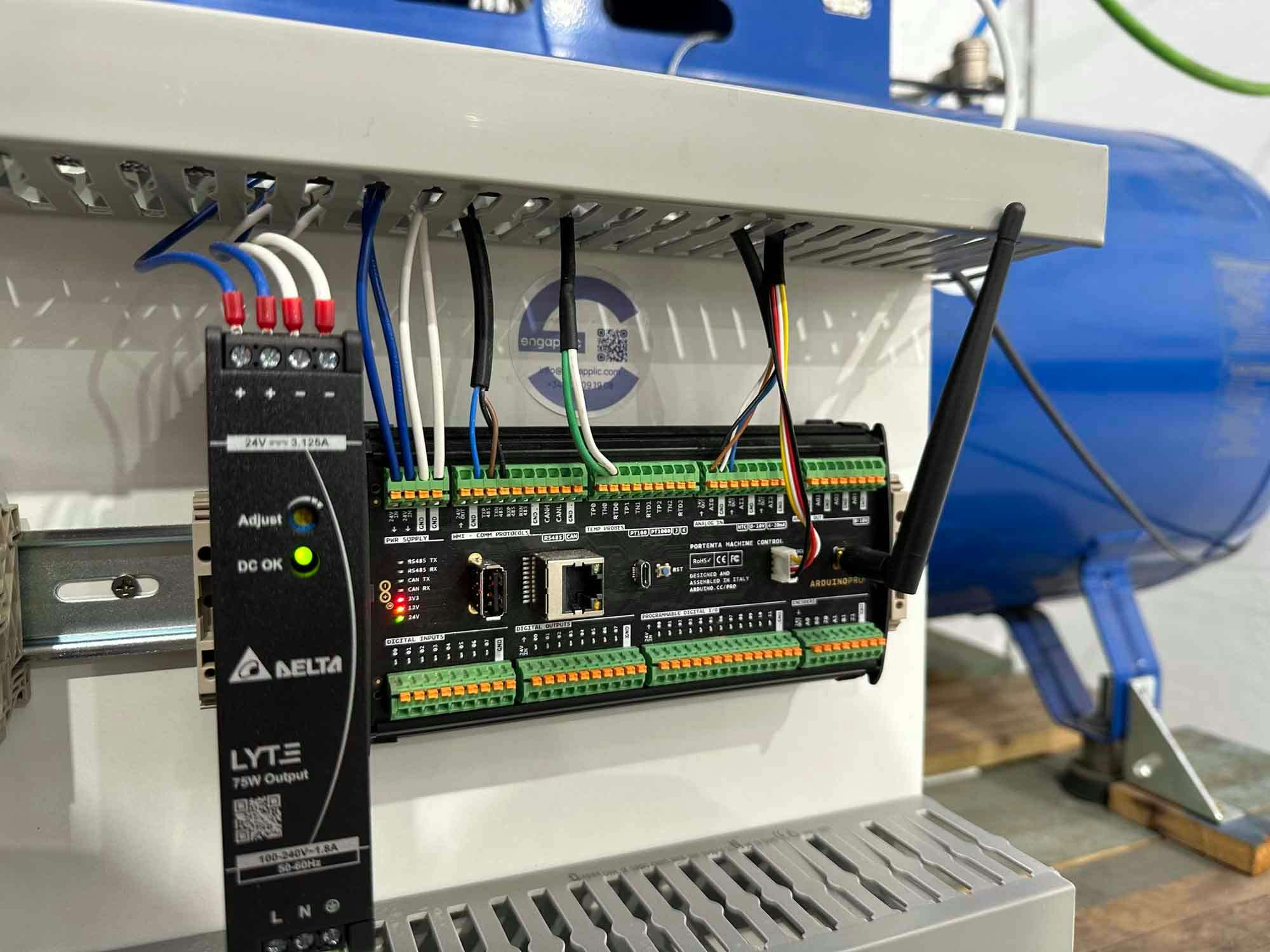
Engapplic put Portenta Machine Control at the heart of its ingenious system to gather a variety of industrial air compressor parameters, monitor the machine’s status via Cloud, optimize use and rationalize maintenance to generate savings – and new business opportunities.
Air compressor temperature, vibration, energy consumption and pressure data are detected via sensors and sent to the Cloud, where they are stored using AWS, to be visualized in real time thanks to Grafana. With its Modbus RTU and TCP/RS485/I2C, thermocouple input and many analog and digital I/Os, Portenta Machine Control was the key to make this system compact and cost-effective. The onboard connectivity avoided long, bulky cables, and DIN-rail compatibility made installation effortless.
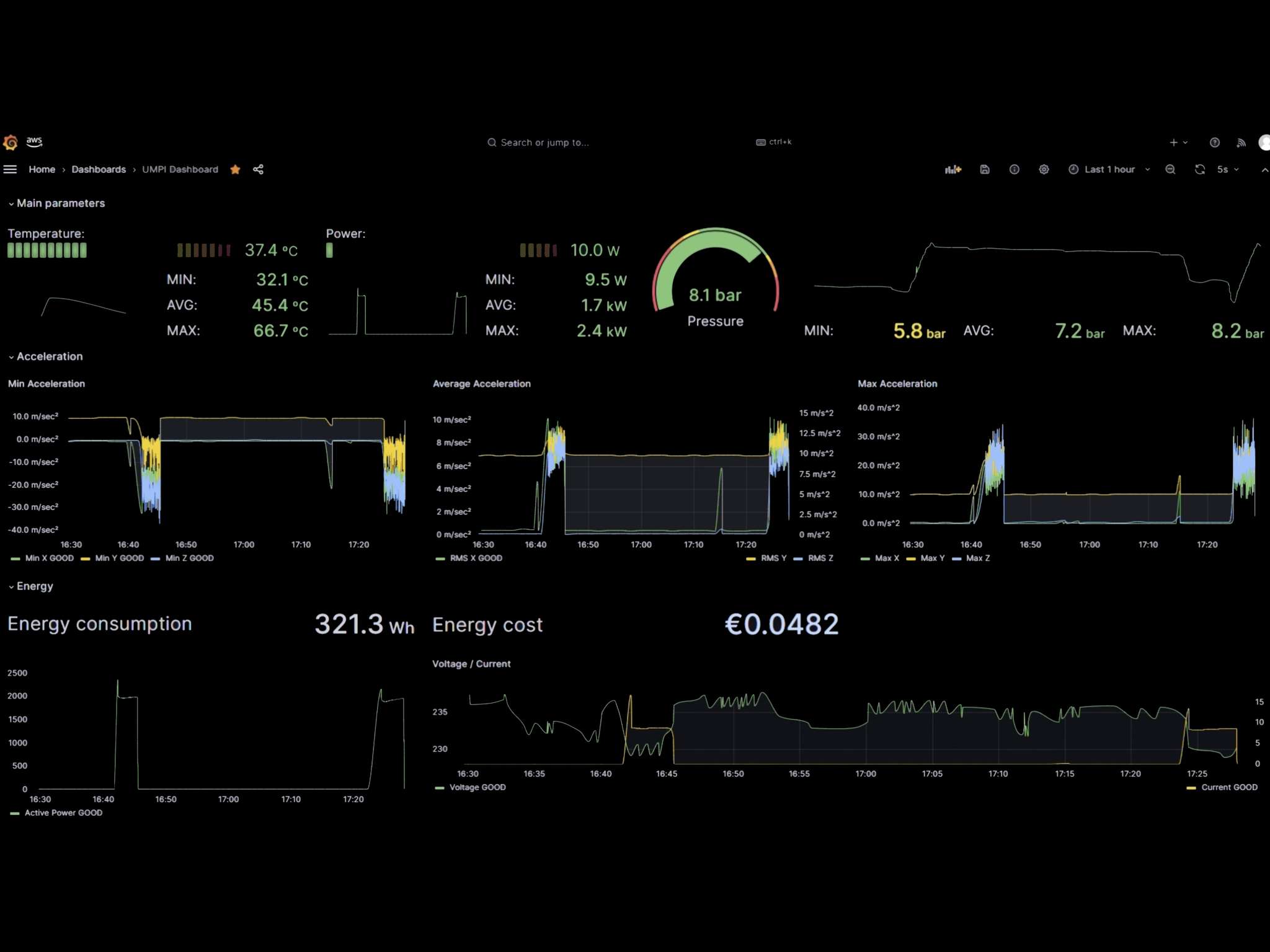
What’s more, working with Portenta Machine Control allowed Engapplic to speed up development by using some of the many, readily available Arduino libraries out there, and to offer the end client a rock-solid and future-proof solution to perform Edge AI functions such as predictive maintenance.
The result? First of all, a huge reduction in machine downtime, also thanks to more timely local support and a better maintenance schedule becoming possible. Second, conspicuous energy saving, cutting the electricity bill by detecting circuit leakages. Finally, and most importantly, a very satisfied client.
The proof of concept was such a success, Engapplic managers are planning to turn it into new business by creating a plug-and-play kit for industrial compressors that other small and medium enterprises would be interested in, on their own path towards Industry 4.0.
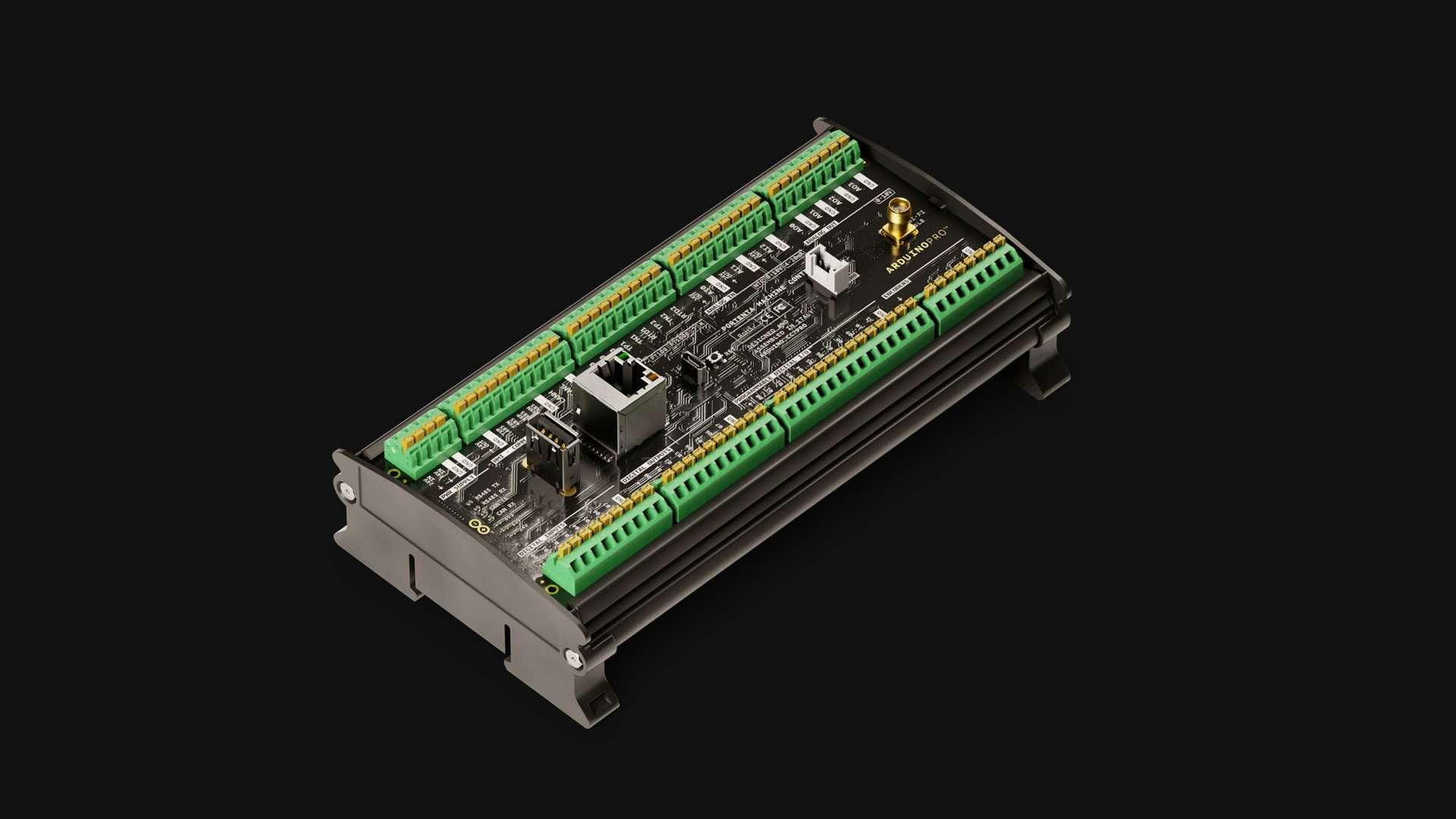
Add IoT capabilities to your industrial machinery, make your products smarter, and develop custom solutions to leverage AI on the Edge with this fully-centralized, low-power, industrial control unit, designed to effortlessly interact with sensors, the Cloud, and more.
Programmable using the Arduino framework or other embedded development platforms, it is the perfect combination of reliable and versatile: discover all the tech specs and some outstanding usage case examples on our dedicated page.