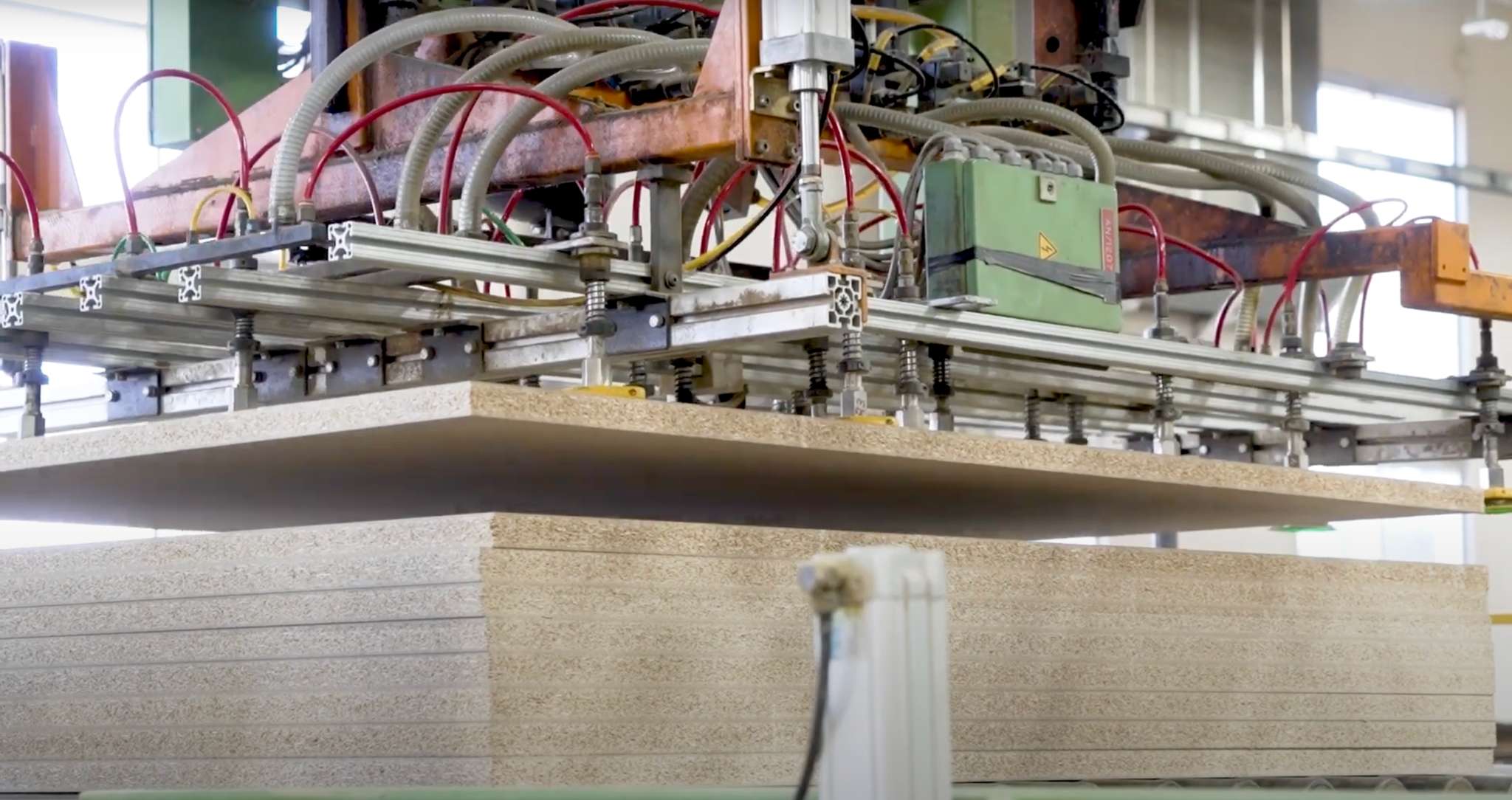
Optimizing the performance of legacy equipment, while enabling data-driven business decisions.
Recently recognized by Fortune among the World’s Most Admired Companies (first in the Home Equipment and Furnishings category), Steelcase is a global design company and thought leader striving to “help people do their best work by creating places that work better”. Founded in 1912, it has developed an extensive catalog of furniture for the office, education spaces and health industry that embody excellence in manufacturing and a forward-thinking vision – which are reflected in their own production process and work environment as well.
Steven Jones and Valerie Miller tell us more about how they improved Steelcase’s day-to-day operations with a simple solution, based on Arduino’s open-source micro PLC: “We were able to wire in the Opta and capture the signals that indicate that the machine’s not performing exactly the way that it should be.” (To find out more about this success story, watch the full-length segment from the 2024 Arduino Days on YouTube.)
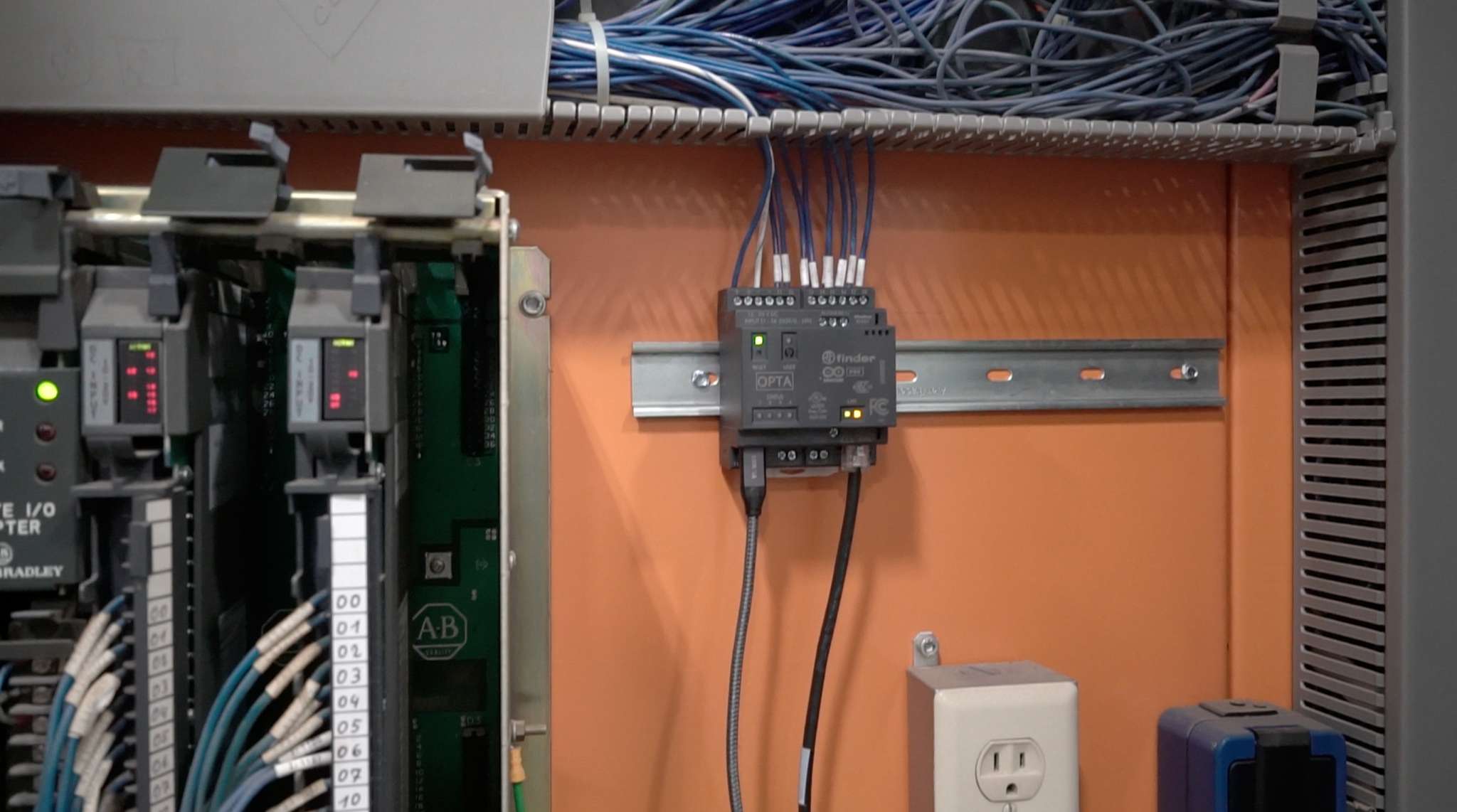
Steven Jones, a technical process consultant at the company, works to develop and deploy the Industrial Internet of Things (IIoT) in all 13 Steelcase plants solving problems using data. When asked to help factory engineers understand why a destacking machine – which takes boards from a stack and places them on a conveyor belt – occasionally underperformed, he searched for a solution that could identify when the problem was occurring and add valuable insights to improve operation from there on out.
“In 2019, we started a reinvention of how we make laminate products within the factory. We essentially created a digital twin for ‘what if’ analysis: IoT allows us to take information in real time and interpret that into what happened, what could we have done differently, and what do we want to continue doing more of – so that we get smarter in our core problem-solving activities.”
– Valerie Miller, Steelcase Operations Engineering Manager
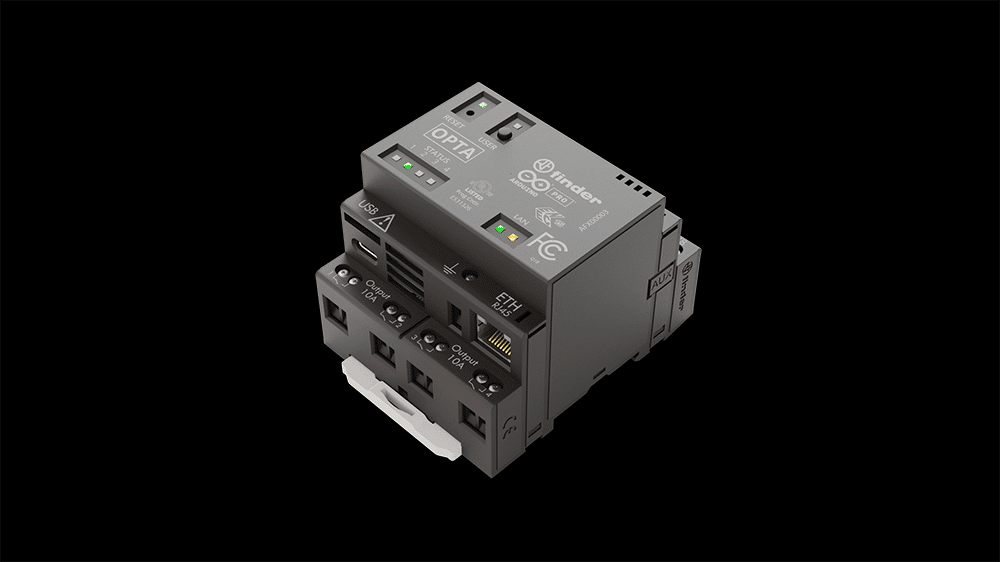
Steelcase improved their workflow by building a simple and cost-effective application around the Arduino Opta.
When a machine seems to not work properly at random, “Traditionally, you’d get a person out there with a stopwatch and a clipboard, but it could be days or weeks before they might see this issue arise,” says Jones. Wiring Arduino’s secure and easy-to-use micro PLC (supporting Arduino programming experience and PLC standard languages) into existing equipment allowed Steelcase to monitor signals that indicate when a specific problem was occurring.
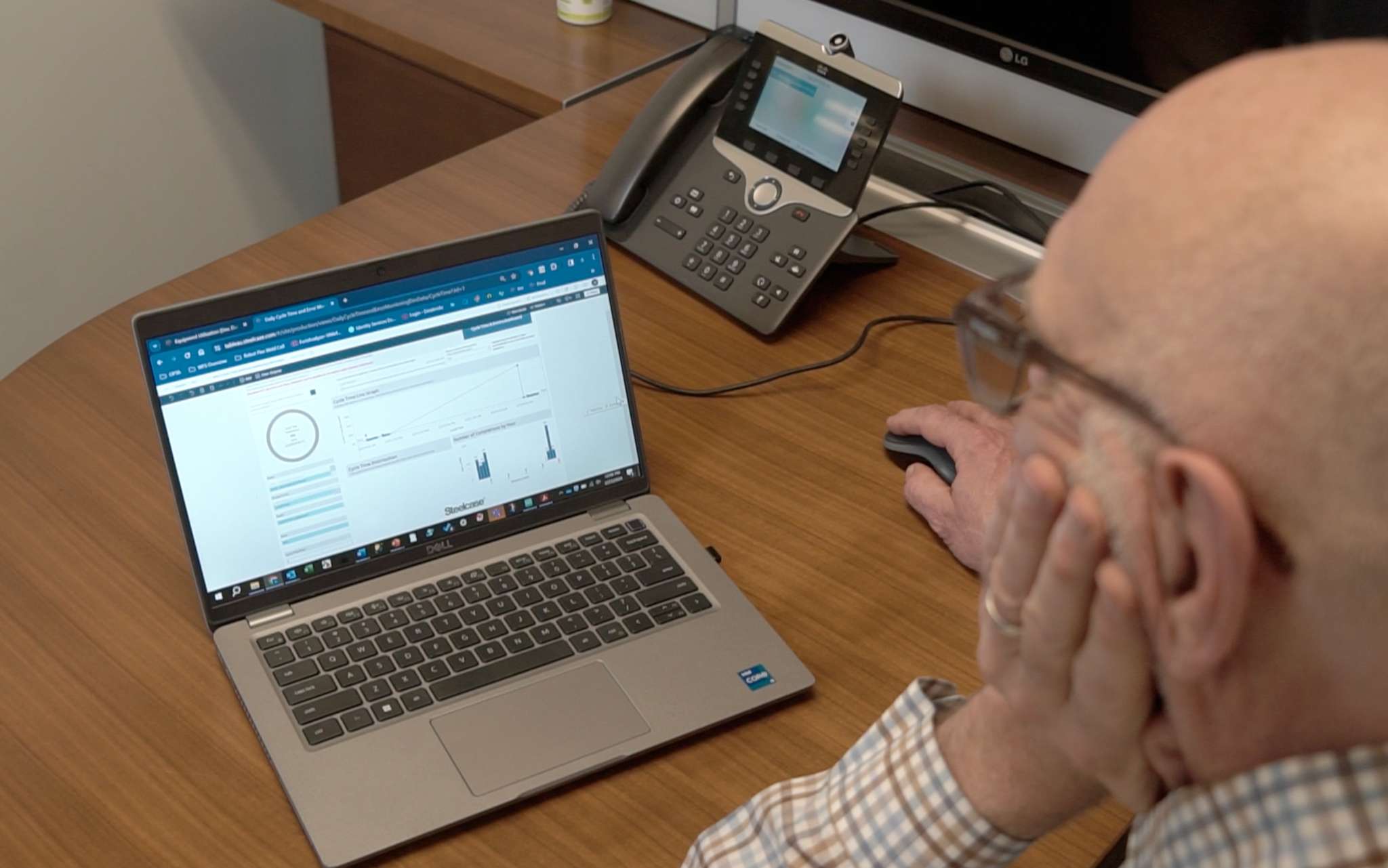
With this information, control engineers, electricians and developers within the company were able to quickly create a solution to provide visibility over any critical IoT events on the machine, via custom dashboards.
“That wasn't so easy to do a decade or so ago, but the IoT tools becoming available are much more cost-effective than they have been in the past. I started working in factories in pre-internet times: the technology now is available to do things that were never imaginable before,” says Jones. “Opta has digital inputs and digital outputs, analog inputs, outputs, everything that a regular PLC would have.”
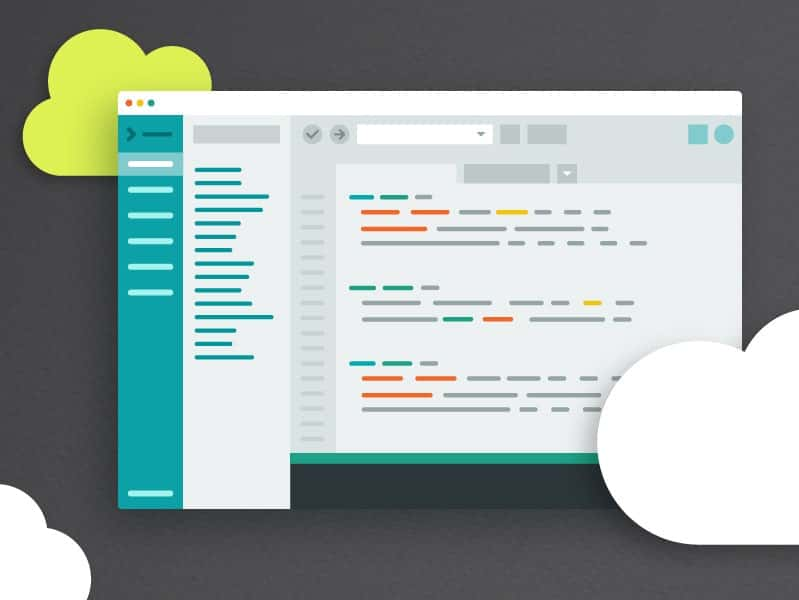
Unlocking the power of data takes leading enterprises from IoT to AI-powered manufacturing.
Industry 4.0 essentially requires embedded systems that connect to the internet, use big data, and finally support decisions about what needs to be done in the factory to achieve better efficiency and productivity: “When you have an idea or an opinion and you can support it with data, you can usually get things to happen much more quickly,” Jones observes. At Steelcase, this will naturally lead to increased use of AI: “We’re positioning ourselves also for the time when machines make decisions. I think if we curate our data appropriately and ask the right questions, it could be revolutionary for us.”