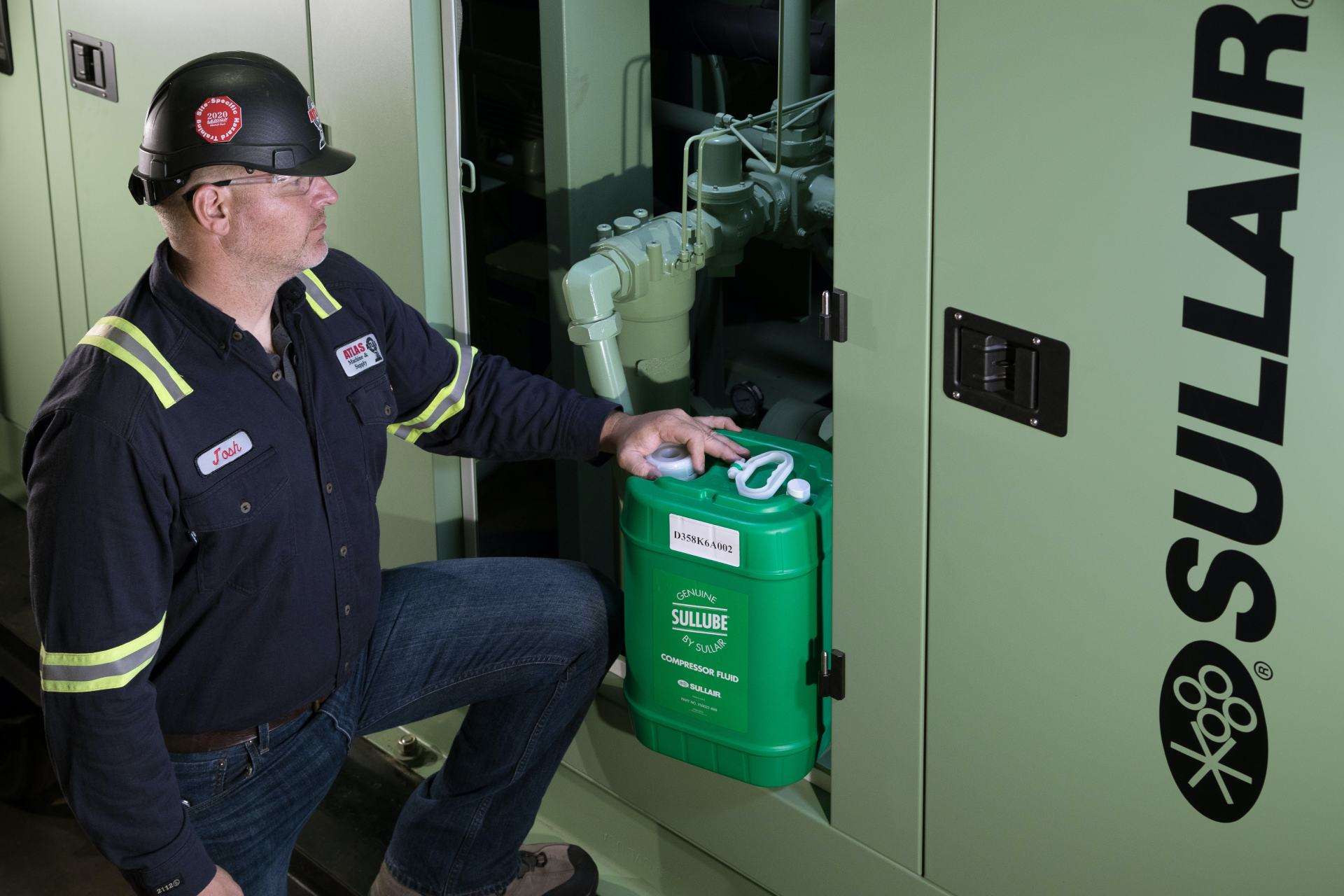
To “fix the biggest machines in the world, anytime and anywhere,” requires remote advanced solutions that build upon decades of technical expertise and the most advanced edge-to-cloud technology.
Headquartered in Louisville, Kentucky, Atlas Machine and Supply, Inc. is a 100-year-old industrial equipment maintenance company and leading service provider in the air compressor industry. Serving clients across the Central US in sectors ranging from manufacturing to healthcare, they faced the challenge of monitoring and maintaining thousands of air compressors spread across various sites.
CEO Richie Gimmel sums up how he discovered Arduino, and how it had a huge impact for Atlas Machine and Supply: “It’s been hugely beneficial to our business, and it’s allowed us to serve our customers better than we did in the past.”
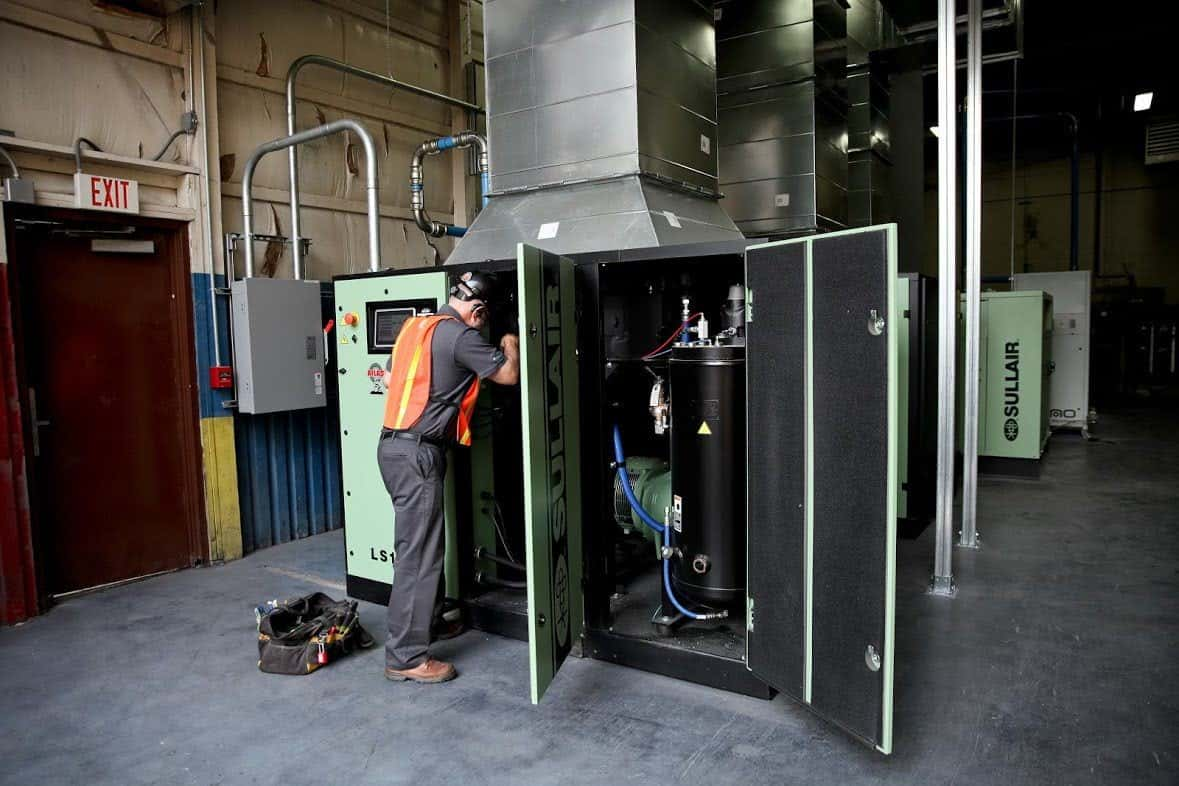
Richie Gimmel, CEO of Atlas, highlighted the limitations they encountered: “These compressors run for 25 years or more, and clients often use multiple brands across their systems. We needed a single, flexible system that could gather uniform, centralized data and provide a unified view across all machines, regardless of brand or age, allowing us to move from reactive to predictive maintenance.”
To meet this challenge, Atlas turned to the Arduino Opta micro PLC as a first step, for its flexibility, cost-effectiveness, and compatibility across different equipment types.
“With Opta and Arduino Cloud, we moved from multiple, isolated data streams to a streamlined, centralized system. The real-time data and integrated dashboard allow our team – and clients – to track system performance seamlessly.” – Richie Gimmel, CEO of Atlas Machine and Supply
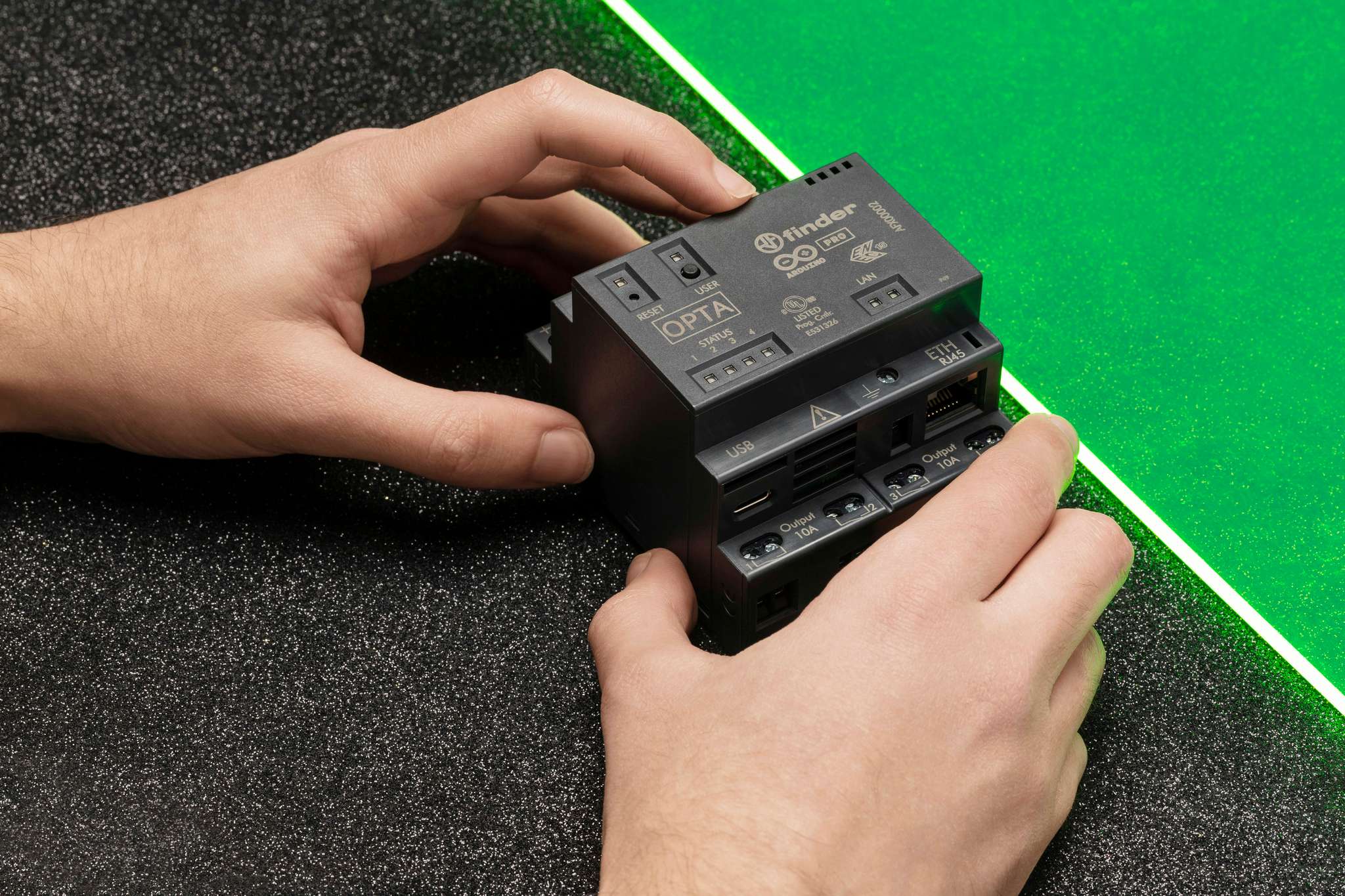
Equipping each air compressor in the fleet with Opta enables real-time monitoring and predictive maintenance, improving service quality and reducing unexpected downtimes.
Critical data like temperature, pressure, service indicators, and energy usage is captured and transmitted to Arduino Cloud running on AWS for robust storage, processing, and data visualization.
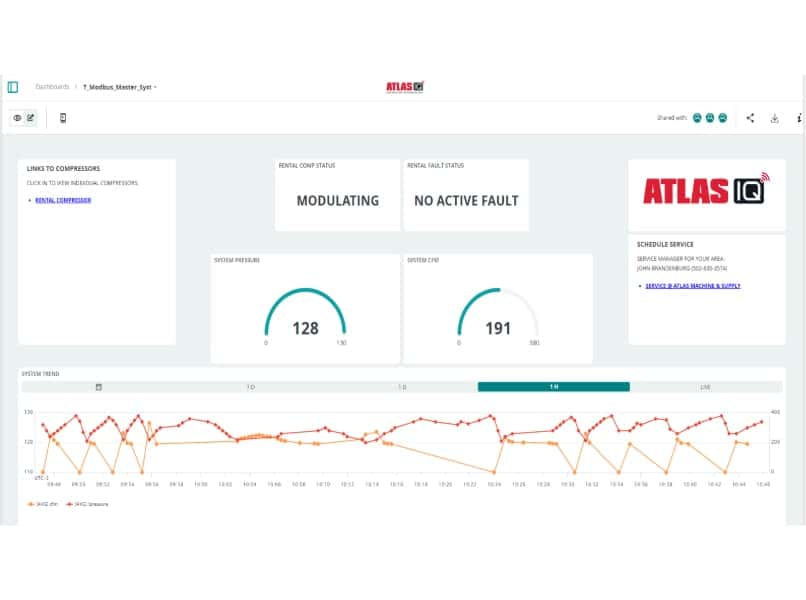
Consolidating data across compressors of various makes and models into a single, user-friendly platform has led to marked improvements in operational efficiency and client satisfaction – further strengthening Atlas’s role as a trusted service provider. Their success with Arduino Opta and Cloud exemplifies how customizable, open-source technology can drive innovation and efficiency in industrial applications.
Image: With this dashboard, Atlas gives clients an at-a-glance overview of how their system is operating. Indicators include compressor status and fault status, system pressure, and CFM (cubic feet per minute) of air delivered.
Atlas Machine and Supply built its solution with Arduino Pro to:
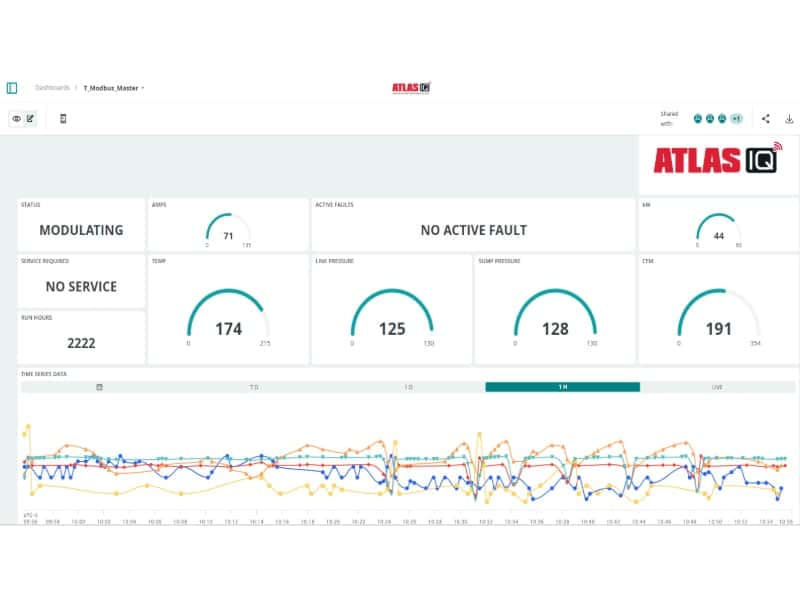
Arduino Cloud has been instrumental in transforming Atlas’s monitoring capabilities.
For Atlas, integrating with AWS was crucial in selecting a platform, as many of their internal business operations rely on AWS services. They needed a solution that would not only support data storage in AWS but also seamlessly connect with tools like Tableau for real-time visualizations. Arduino Cloud, with its AWS compatibility, allowed Atlas to unify their data and workflows in a single ecosystem.
Image: This dashboard offers a comprehensive view of essential machine metrics for both Atlas and its customers. Key insights include fault status, service requirements, run hours, and compressor status.
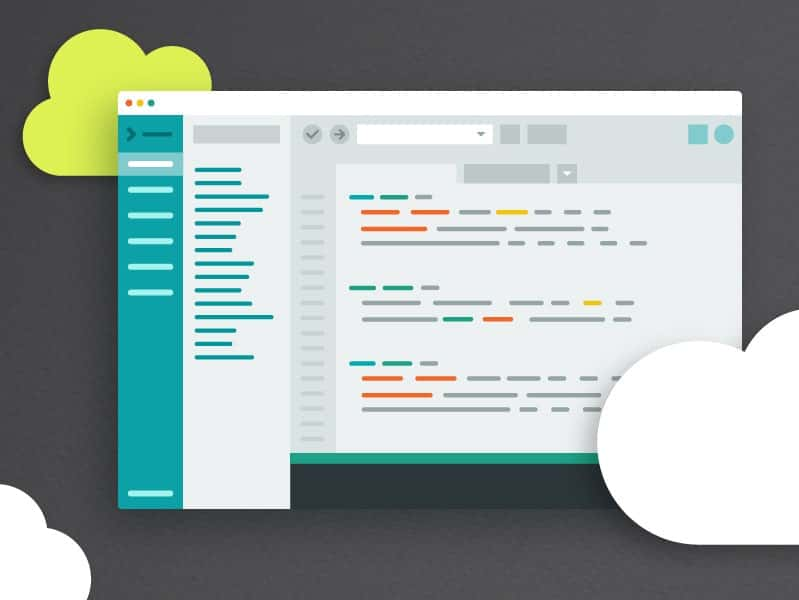
Now, thanks to Arduino Cloud’s low-code approach to creating dashboards, performing device lifecycle management and over-the-air (OTA) updates, and data export capabilities, Atlas has achieved a seamless monitoring experience. Gimmel shared, “Arduino Cloud has changed how we interact with data. The OTA updates, close-to-real-time data, and ability to build and share customized dashboards with clients have made it a complete game-changer. The reliability of Arduino Cloud means fewer devices go offline, and it allows us to deploy new devices confidently.”